Definition of CNC lathe
CNC Swiss lathe is a lathe that originated in Switzerland and is known internationally as Swiss precision automatic lathe.The vast majority of cnc machines perform turning in the form of longitudinal cutting, hence they are also known as longitudinal cutting CNC lathes in the Chinese market.Due to the standard configuration of CNC turning and milling machines with side power heads, they can complete milling processes, also known as CNC turning and milling composite lathes.

The difference between Swiss-type lathe and CNC cutting machine
Both are CNC horizontal lathes. Traditional CNC lathes are mainly cutting, so they are called cutting lathes.
According to the loading and clamping methods, they can be divided into: mechanical arm, bar feeder, manual loading, etc.; but the product’s single clamping position remains unchanged, and it is impossible to feed multiple times. The product can only be processed by rotating the spindle C axis and moving the tool holder Z/X/Y. For long-axis products, only the end face can be supported by the ejector and the bracket can be installed, but it is difficult to achieve the ideal accuracy and complete the product process requirements at one time.
Swiss-type lathe is a cutting method that processes products by moving the spindle Z axis and rotating the C axis, and the tool remains in a fixed position. The machine supports multiple feeding methods, and theoretically can process products with a length up to the maximum length of a single material supported by the feeder.
The longest single product produced by Jianke centrifuge is made of 45# stainless steel, with a diameter of 20mm and a length of 1780mm.
In a CNC lathe, the bar is fed axially through a central guide sleeve, and the cutting tool is located right next to the guide sleeve opening, which is extremely rigid and eliminates any deformation caused by cutting pressure. This allows impressive precision work to be performed with high efficiency, ensuring absolute accuracy of the finished part.
Compared with traditional processing machines, CNC lathes have an absolute advantage when processing slender shaft parts. Overall, CNC lathes are an excellent choice for those who want to achieve excellent results when processing long shaft parts.

Requirements of Raw Materials for Swiss-Style Lathes
Swiss-style lathes, under normal circumstances, only support long bar stock (individual rods of 2-4 meters in length) for bulk processing. Unlike cutting lathes, they cannot process short pieces or single items.
Additionally, due to the bar stock needing to pass through the entire spindle and chuck, precision in straightness and ovality of the raw material is highly required.
Typically, highly polished bar stock of 2-4 meters in length is needed, with a surface roughness not exceeding Ra2.5. The diameter tolerance of the bar stock should be within 0.020mm, with the roundness of each piece being 1/3 to 1/2 of the minimum tolerance size of the finished product, and with a variation in taper of less than 0.020mm.
diameter and straightness | Allowable range | |||||
Large bending every 1000mm | small bending every 300mm | |||||
Grade A | Grade B | Grade C | Grade A | Grade B | Grade C | |
Φ Below 3mm | / | / | / | Within0.025mm | Within0.05mm | / |
Φ3-Φ10mm | Within 0.25mm | Within 0.5mm | Within1mm | Within0.1mm | ||
Φ10-38mm |
The above tables and parameters are only applicable to the vast majority of products and materials and are for reference only. According to the tolerance requirements and process arrangement of the final product, the requirements for raw materials can be appropriately relaxed or tightened during actual processing.
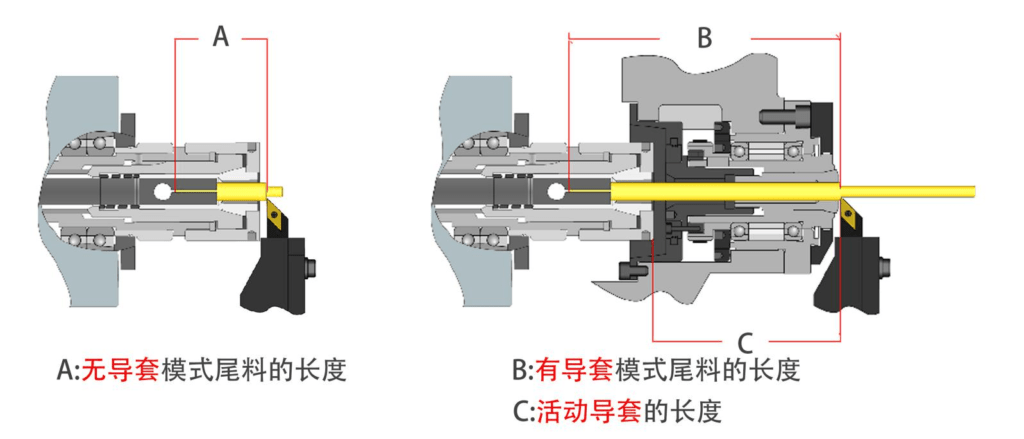
The difference between the guide sleeve mode and the non guide sleeve mode of the centrifuge
Due to the use of long bar materials in the machining of the centrifuge, there is a need to leave a margin at the end of the entire material to provide space for the fixture to clamp. Therefore, there is a disadvantage of waste of tailings in the machining of the centrifuge.
The entire series of Jianke CNC machines have the function of freely switching between cutting modes with guide sleeve and without guide sleeve .
Structure of the machining area of the CNC machine
The structure of the main processing area of the CNC machine is composed of a spindle (sub spindle) and a tool holder.
Spindle: Equipped with Z-1 axis movement and C-1 axis arbitrary indexing rotation and positioning, supporting multiple feeding;
Auxiliary spindle: Equipped with Z 2 and X 2 axis movement and C2 axis arbitrary indexing rotation and positioning, assisting in spindle processing, material receiving, and completing subsequent processes of products on the corresponding tool holder of the auxiliary axis. During the processing, independent control channels are used to complement and intervene with the spindle, achieving simultaneous processing of two spindles and shortening the overall processing efficiency of the product.
Knife holder:
- Turning tool: located on the spindle tool holder, it can achieve processes such as turning groove, turning outer diameter, turning thread, and cutting.
- Side power head: Located on the spindle tool holder, the product can be processed by drilling, tapping, sawing, milling flat, milling groove and other processes. Some models support plug-in expansion functions, and can be equipped with mechanisms such as end power head, cyclone milling, and angle power head to meet more complex process requirements.
- End face fixed seat: located on the end face of the spindle tool holder, centered around the product center and rotating with the spindle C1 axis, it can meet the process requirements of drilling, tapping, and boring the product.
- Auxiliary shaft end milling seat: located on the auxiliary shaft tool holder, the Y2 axis of the tool holder is matched with the X2, Z2 axis, and C2 axis of the auxiliary main shaft to perform drilling, tapping, sawing groove, milling flat, milling groove, and other processing processes on the product. All series models support plug and insert expansion functions.
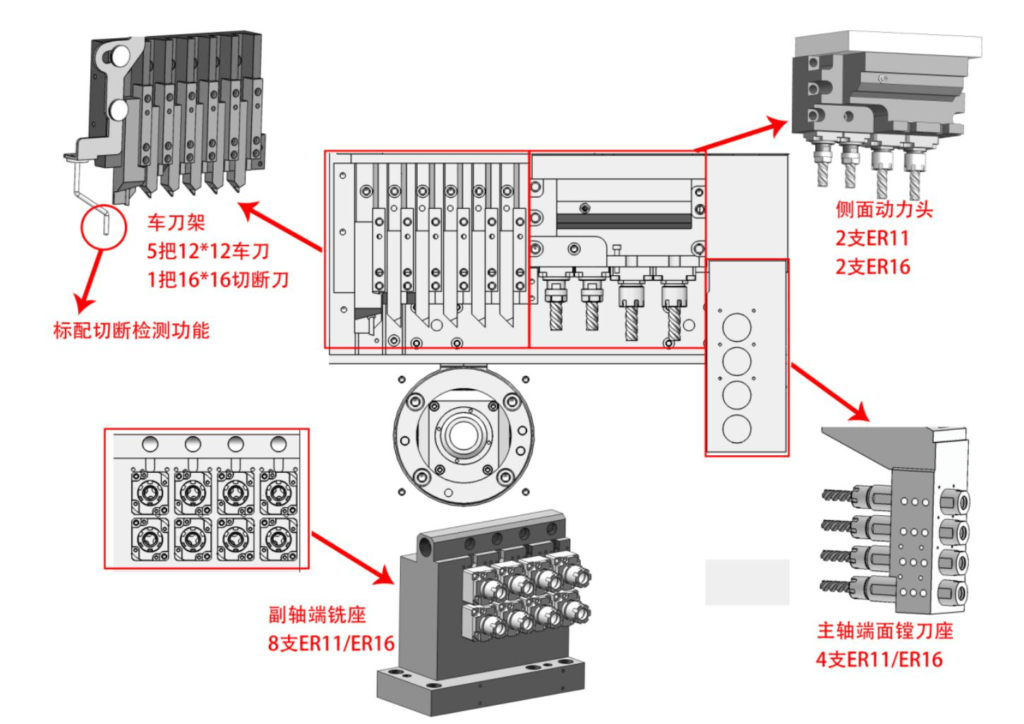
Model of centrifuge
The model naming of a centrifuge is generally based on the maximum machining diameter, number of spindles, and number of moving axes of the equipment as reference naming.
Processing diameter range
Due to the use of long bars as raw materials in the processing of the cnc machine, and the raw materials passing through the spindle, in order to ensure more stable processing accuracy, the cnc machine determines the processing range based on factors such as eccentricity, spindle power, and spindle speed of materials with different diameters.At present, the maximum diameter models of domestically produced cnc machines in China are 12, 16, 20, 25/26, and 32mm.
Number of moving axes and spindles
- Conventional centering machines are divided into single spindle CNC centering machines and dual spindle CNC centering machines based on the number of spindles.
- The single spindle cnc machine is composed of the Z-axis of the spindle and the X-axis and Y-axis of the tool holder, so
- It is called a three-axis centrifuge and comes standard with a turning tool, side power head, and end boring tool holder, controlled by a system channel.
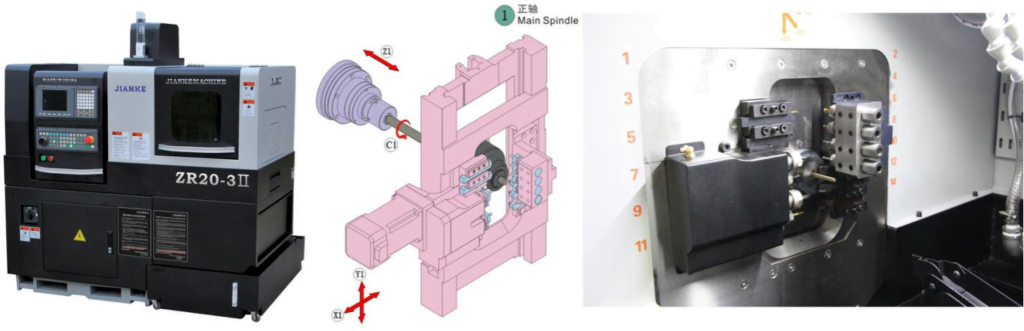
Double spindle CNC machine tool
In addition to the X, Y, and Z moving axes of a single spindle cnc machine, a dual spindle cnc machine has added a secondary spindle and multiple moving axes. Controlled by two or more independent system channels, more complex and diverse products can be achieved.
In terms of processing capacity, a single spindle cnc machine can only complete the process of five faces of the product, and the cutting section cannot be processed. Moreover, when cutting the product, due to the influence of the eccentricity during product rotation and the self weight of the product, the product has already broken due to centrifugal force and self weight before the cutting knife passes through the center point of the product, resulting in tail nails and burrs. For products with high requirements, secondary treatment and deburring are required, This drawback cannot be avoided by all single spindle lathes.
On the basis of completing the process with a single spindle, the dual spindle cnc machine receives the product from the main spindle and processes the sixth surface on the tool holder of the auxiliary spindle. At the same time, as the auxiliary spindle is an independent channel, after the auxiliary spindle receives the product from the spindle, the spindle immediately starts processing the next product. The auxiliary spindle runs at the same time to process the sixth surface, with both sides running simultaneously, greatly reducing the overall processing efficiency.
At present, China’s domestically produced conventional centrifuge has a maximum of six moving axes. In 2015, Nanjing Jianke Machinery independently developed and invented a nine axis CNC cnc machine that supports up to nine moving axes. It is controlled by three independent channels and has obtained invention patents, representing the highest level of Chinese cnc machines.
The conventional naming format for Swiss-type lathes by different manufacturers is (maximum machining diameter) – (number of movable axes). For example, if the maximum machining diameter is 20mm, a single spindle lathe would be named 20-3, while a dual-spindle lathe would be named 20-4, 20-5, and so on. This standardized naming convention helps customers easily identify and select the right machine for their specific needs. With this innovation in precision machining technology, manufacturers can continue to meet the evolving demands of their customers and achieve new levels of success in their industries.
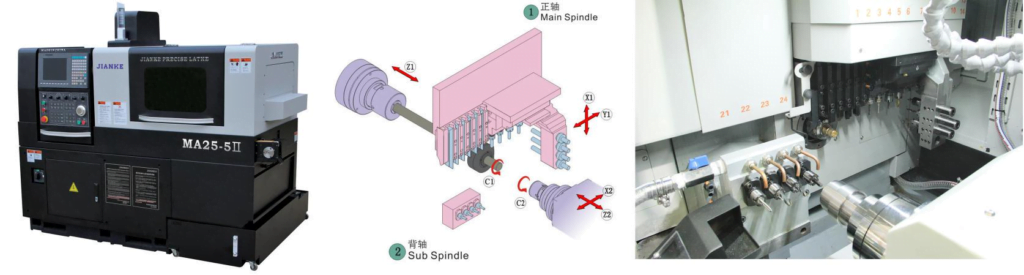
Knife holder arrangement structure and its advantages and disadvantages
The arrangement of the tool holder of the cnc machine is divided into side row structure and horizontal row structure based on the cutting direction of the turning tool.
Side row knife
Advantage: Due to the average distribution of tools on both sides, the switching stroke between tools is short. For products with a large number of tools and frequent tool switching, there is a slight saving in processing efficiency.
Disadvantage: The cutting tool cuts through the side, which can easily cause chips to wrap around materials that are difficult to break (such as aluminum), causing the equipment to alarm and stop processing.The cutting tools are arranged tightly and cannot be extended using the pull and insert function.
Horizontal knife
Advantages: The cutting tool cuts in from above, which is easier to remove chips and has stronger cutting toughness compared to the side cutting structure.The cutting tools are arranged in a straight line, with ample spacing between the power heads, supporting various insertion and expansion functions.
Disadvantage: Due to the fact that the tools are all above the tool holder, the tool stroke is longer. Compared to the side row tool structure, when switching tools frequently, the time spent is slightly increased.
Feeding mechanism
The cnc machine only supports the processing of long bar material feeding, and the long bar material will move in and out with the movement of the spindle, so the feeding machine of the cnc machine is different from the feeding machine of the conventional cnc machine.
The feeding machines suitable for cnc machines are divided into chain type feeding machines and oil film type feeding machines.
Chain feeding is relatively inexpensive and suitable for enterprises with low product accuracy requirements and no requirements for environmental noise pollution.
The oil film feeder ensures the stability of material rotation and reduces noise pollution caused by high-speed rotation of materials by sealing the material in the material groove and continuously injecting lubricating oil into the groove.

The advantages of a centrifuge CNC lathe
- Long term automated operation: With the automatic feeding and material changing of the feeding machine, it can achieve 24-hour startup operation, excluding tool replacement, maintenance and other work tasks. The actual processing operation time can reach 20-22 hours;
- Labor saving: The centrifuge can complete composite processing such as turning, milling, drilling, boring, tapping, carving, etc. at the same time, integrating traditional multiple types of equipment into separate processing processes. By replacing multiple equipment with one equipment, one person can view 5-10 centrifuge machines, reducing labor costs;
- Improving the pass rate: Due to the integration of turning, milling, and automation, the consistency of product processing is stronger, avoiding precision deviation caused by multiple clamping processes, and reducing the high scrap rate of products caused by factors such as worker sentiment. The cnc mode of the cnc machine ensures the accuracy requirements of shaft products, which cannot be replaced by traditional cnc machines;
- High efficiency: The processing method of multi-channel and multi spindle operation effectively improves the processing efficiency of products and creates more product value for customers.
Application fields of centrifuge CNC lathe
The combination of the cnc machine and the automatic feeding machine can achieve 24-hour operation. Based on the characteristics of the cnc machine, which can simultaneously complete composite processing such as turning, milling, drilling, boring, tapping, carving, etc., it can complete multiple batches and high complexity products at once, greatly saving labor costs, improving processing efficiency, and product qualification rate. The centrifuge is mainly used for batch processing of precision hardware, shaft shaped non-standard parts in industries such as medical, military, automotive, hardware, electronics, clocks, communication, etc.