CNC (Computer Numerical Control) lathes have revolutionized the manufacturing industry, offering unparalleled precision, efficiency, and versatility in machining operations. These sophisticated machines have become indispensable tools for businesses looking to streamline their production processes and deliver high-quality products consistently. In this comprehensive guide, we will delve into the world of CNC lathes, exploring their components, working principles, applications, and best practices for maintenance and operation.
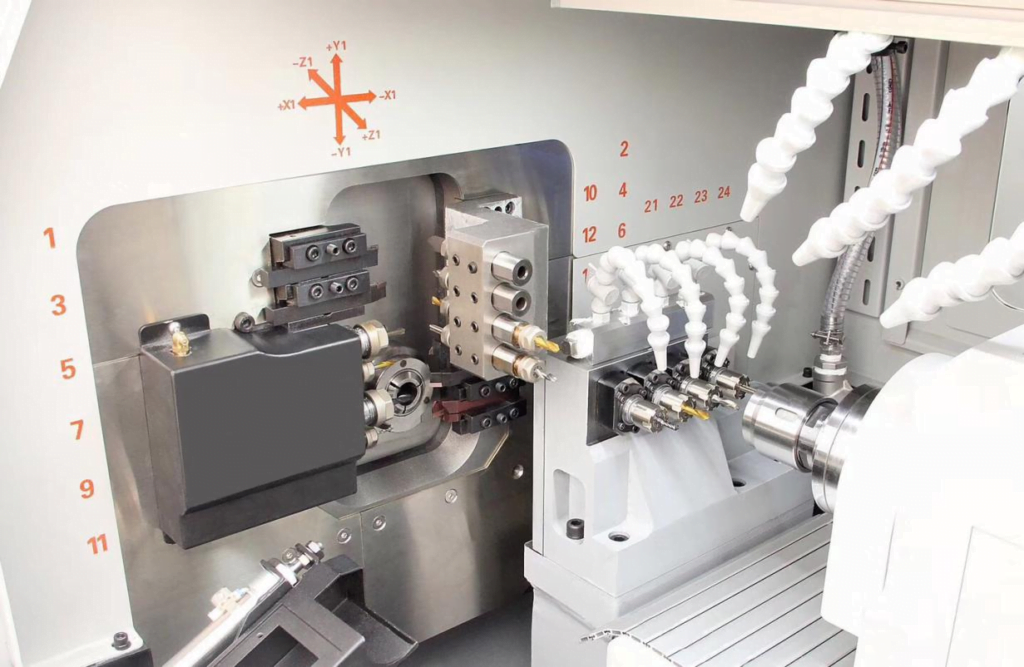
What is a CNC Lathe?
A CNC lathe is a computer-controlled machine tool that performs turning operations on a rotating workpiece. Unlike traditional manual lathes, CNC lathes are fully automated and operate based on pre-programmed instructions, eliminating the need for constant operator intervention. These machines are capable of producing complex and intricate parts with exceptional accuracy and repeatability.
Key Components of a CNC Lathe
- Headstock: The headstock houses the main spindle, which holds and rotates the workpiece. It also contains the spindle drive system, consisting of motors and gears.
- Lathe Bed: The lathe bed serves as the foundation of the machine, providing a stable platform for the headstock, tailstock, and carriage to move along.
- Carriage: The carriage, also known as the saddle, moves along the lathe bed and carries the cutting tool. It consists of the cross slide and the compound rest.
- Tailstock: The tailstock is mounted on the opposite end of the lathe bed and supports the free end of the workpiece. It can be moved along the bed to accommodate different workpiece lengths.
- Tool Turret: The tool turret, or tool post, holds multiple cutting tools and can be rotated to switch between tools during machining operations.
- CNC Control System: The CNC control system is the brain of the machine, consisting of a computer, control panel, and software. It interprets G-code instructions and controls the motion of the machine axes.
Working Principle of CNC Lathes
CNC lathes operate based on a series of precise, computer-controlled movements. The process begins with the creation of a 3D CAD model of the desired part. This model is then converted into G-code, a programming language that provides instructions for the machine’s movements and operations.Once the G-code is loaded into the CNC control system, the machine executes the programmed instructions. The workpiece is securely held in the chuck, which is mounted on the spindle. As the spindle rotates the workpiece, the cutting tool, held in the tool turret, moves along the lathe bed and engages with the workpiece, removing material to create the desired shape.The CNC control system continuously monitors and adjusts the position and speed of the cutting tool, ensuring high precision and accuracy throughout the machining process. The machine can perform a wide range of turning operations, including facing, boring, threading, grooving, and contouring.
Applications of CNC Lathes
CNC lathes find applications across various industries, including:
- Automotive: CNC lathes are used to manufacture engine components, transmission parts, and other precision automotive components.
- Aerospace: These machines are employed in the production of aircraft parts, such as turbine blades, landing gear components, and structural elements.
- Medical: CNC lathes play a crucial role in the manufacturing of medical devices, implants, and surgical instruments, where high precision and accuracy are paramount.
- Electronics: CNC lathes are used to produce electronic components, such as connectors, housings, and heat sinks.
- Oil and Gas: These machines are utilized in the fabrication of drilling components, valves, and other precision parts for the oil and gas industry.
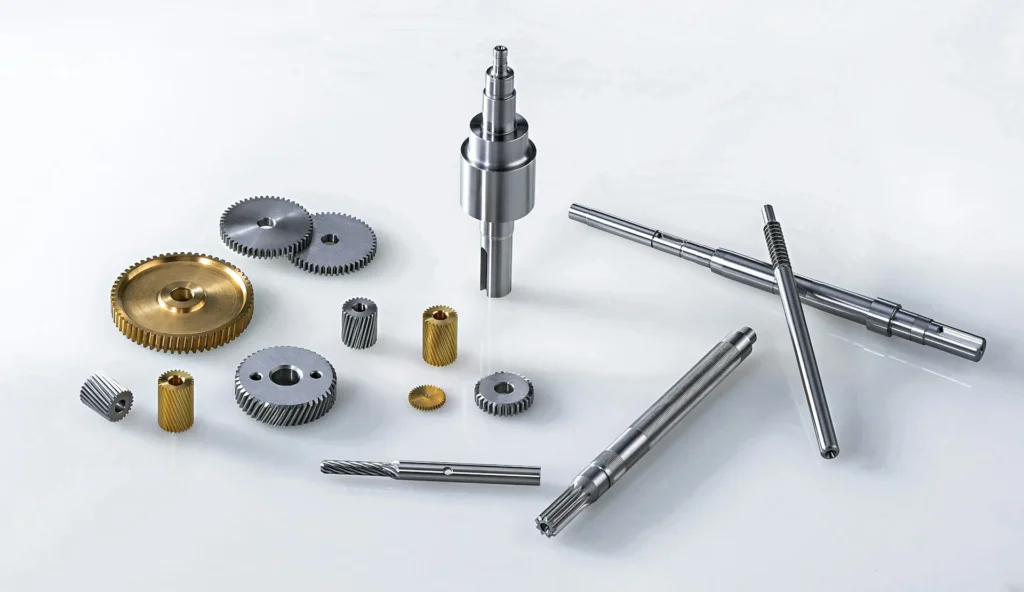
Maintenance and Best Practices
Regular maintenance and adherence to best practices are essential for ensuring the longevity, reliability, and optimal performance of CNC lathes. Some key maintenance tasks and best practices include:
- Daily inspections: Conduct thorough inspections of tooling, lubrication levels, and coolant levels on a daily basis.
- Weekly and monthly tasks: Perform tasks such as cleaning the machine, inspecting and adjusting slideways, and checking the accuracy of the machine at regular intervals.
- Lubrication: Ensure proper lubrication of all moving parts, including spindles, ball screws, and guideways, as per the manufacturer’s recommendations.
- Coolant management: Maintain the correct concentration and cleanliness of the coolant to prevent bacterial growth and ensure optimal cooling performance.
- Spare parts inventory: Keep a stock of critical spare parts to minimize downtime in case of breakdowns or wear.
- Training and skill development: Invest in training and skill development for operators to ensure proper machine operation and maintenance.
- Predictive maintenance: Implement predictive maintenance techniques, such as vibration analysis and machine monitoring, to identify potential issues before they lead to breakdowns.
Conclusion
CNC lathes have transformed the manufacturing landscape, enabling businesses to produce high-quality parts with unmatched precision and efficiency. By understanding the components, working principles, and applications of these machines, and by implementing proper maintenance practices, manufacturers can harness the full potential of CNC lathes to drive their success in today’s competitive market.As technology continues to advance, CNC lathes are poised to play an even more significant role in shaping the future of manufacturing. Embracing these powerful tools and staying at the forefront of technological advancements will be key to remaining competitive and meeting the ever-evolving demands of the industry.