The Importance of CNC Centering Machine
CNC centering machine WR20-9Ⅱ are the unsung heroes of modern manufacturing. They ensure precise alignment of workpieces, enabling high-efficiency production with minimal errors. Industries like automotive, aerospace, and medical device manufacturing rely heavily on these machines to meet exacting standards. Imagine trying to assemble an engine without perfectly aligned parts—performance would plummet, and safety could be compromised. CNC centering machine WR20-9Ⅱ eliminate such risks by providing unparalleled accuracy.
What sets these machines apart is their ability to work seamlessly with CNC lathe machine cutting tools and CNC machine cutting tools, which are designed for high-precision tasks. For example, in automotive manufacturing, CNC centering machines ensure that critical components like crankshafts and camshafts are perfectly aligned, directly impacting vehicle performance and durability. Their role in reducing production time while maintaining consistency makes them indispensable in any high-volume production line.
What Tools Do CNC Machine Use to Control Tool Movement?
CNC centering machine WR20-9Ⅱ rely on a combination of servo drive systems and linear guides to control tool movement with precision. Think of the servo drive system as the brain that dictates the tool’s position and speed, while linear guides act as the muscles, ensuring smooth and stable motion. Together, they allow the machine to execute even the most intricate designs with ease.
But that’s not all—these machines also depend on specialized tools like CNC lathe machine tools and CNC machine deburring tools to perform cutting, shaping, and finishing tasks. For instance, in aerospace manufacturing, deburring tools remove tiny imperfections from components like turbine blades, ensuring they meet stringent safety and performance standards. Without these tools, achieving the required level of precision would be nearly impossible.
To put it into perspective, imagine crafting a delicate sculpture with a dull chisel—it’s not just inefficient; it’s impossible to achieve fine details. Similarly, CNC machines need these advanced tools to deliver exceptional results in industries where even a millimeter can make or break a product.
Which CNC Machines Can Rotate Grinding Tools?
Not all CNC centering machine are created equal—some models come equipped with rotating spindles or multi-functional heads, allowing them to rotate grinding tools. This feature transforms a standard CNC machine into a versatile powerhouse capable of both cutting and grinding operations.
Take mold-making as an example. A CNC machine with grinding capabilities can polish mold surfaces to perfection, eliminating defects that could ruin the final product. These machines often pair with high-performance CNC machine cutting tools to handle complex tasks efficiently. In medical device manufacturing, rotating grinding tools are used to create ultra-smooth surfaces on components like surgical implants, where precision isn’t just desirable—it’s life-saving.
This versatility makes these machines a wise investment for manufacturers looking to expand their capabilities without purchasing multiple pieces of equipment.
How to Replace Tools in a CNC Centering Machine
Replacing tools in a CNC centering machine might sound intimidating at first, but it’s a straightforward process if done correctly. Start by ensuring the machine is powered off completely—safety first! Then use the appropriate wrench or tool to loosen the bolts securing the old tool in place.
When installing a new tool, alignment is everything. Even a slight misalignment can compromise machining accuracy or damage the workpiece. For example, if you’re using CNC lathe machine cutting tools for hard materials or CNC machine deburring tools for finishing edges, proper alignment ensures optimal performance.
Once installed, always perform a test run before full-scale operation. This step acts as a quality check to confirm that everything is functioning smoothly. It’s like trying on new shoes before going for a long walk—you want to make sure they fit perfectly before committing.
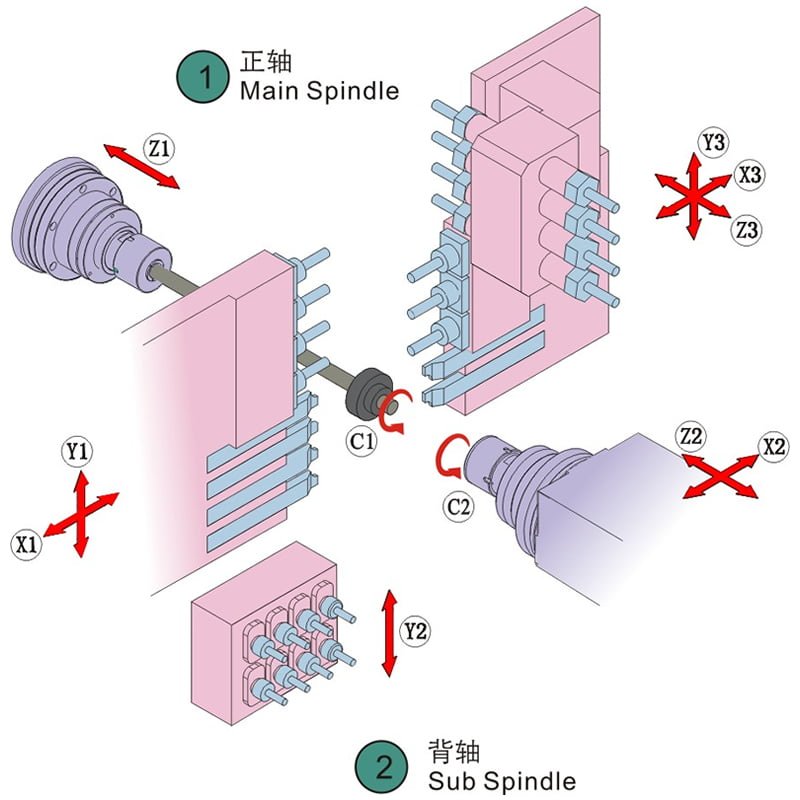
How to Install and Maintain a CNC Centering Machine
Installing and maintaining your CNC centering machine is crucial for ensuring its long-term performance. Start by placing the machine on a flat, stable surface in a clean environment free from dust and debris. Follow the manufacturer’s manual carefully when connecting power and air supplies—skipping steps here could lead to costly mistakes later.
Maintenance is where many users fall short. Daily cleaning is essential; use specialized CNC machine cleaning tools like brushes or vacuums to remove chips and grease buildup. Neglecting this step can lead to mechanical issues over time. Periodic checks of key components such as servo motors, lubrication systems, and coolant levels are equally important.
For instance, an automotive parts manufacturer reduced equipment downtime by 30% simply by implementing weekly deep cleaning sessions and monthly inspections. These proactive measures not only extend the life of your machine but also keep production running smoothly—a win-win for any business.
FAQ
Can CNC centering machines handle complex shapes?
Absolutely! With advanced software controls and high-quality tools like CNC lathe machine tools, these machines excel at processing intricate designs with remarkable precision.
How do I choose the right CNC centering machine?
Consider your specific needs: Are you looking for grinding capabilities? Do you need high-speed operations? For example, if your workflow involves polishing surfaces, opt for models with rotating grinding tool functionality.
What tools can help clean CNC equipment?
Specialized cleaning tools such as brushes, vacuums, or air guns are ideal for routine maintenance. Using dedicated CNC machine cleaning tools ensures even hard-to-reach areas stay spotless.
Why are deburring tools important?
Deburring tools like CNC machine deburring tools enhance surface quality by removing imperfections that could affect assembly or performance—especially critical in industries like aerospace or medical devices where precision is non-negotiable.